GreenBone Technology
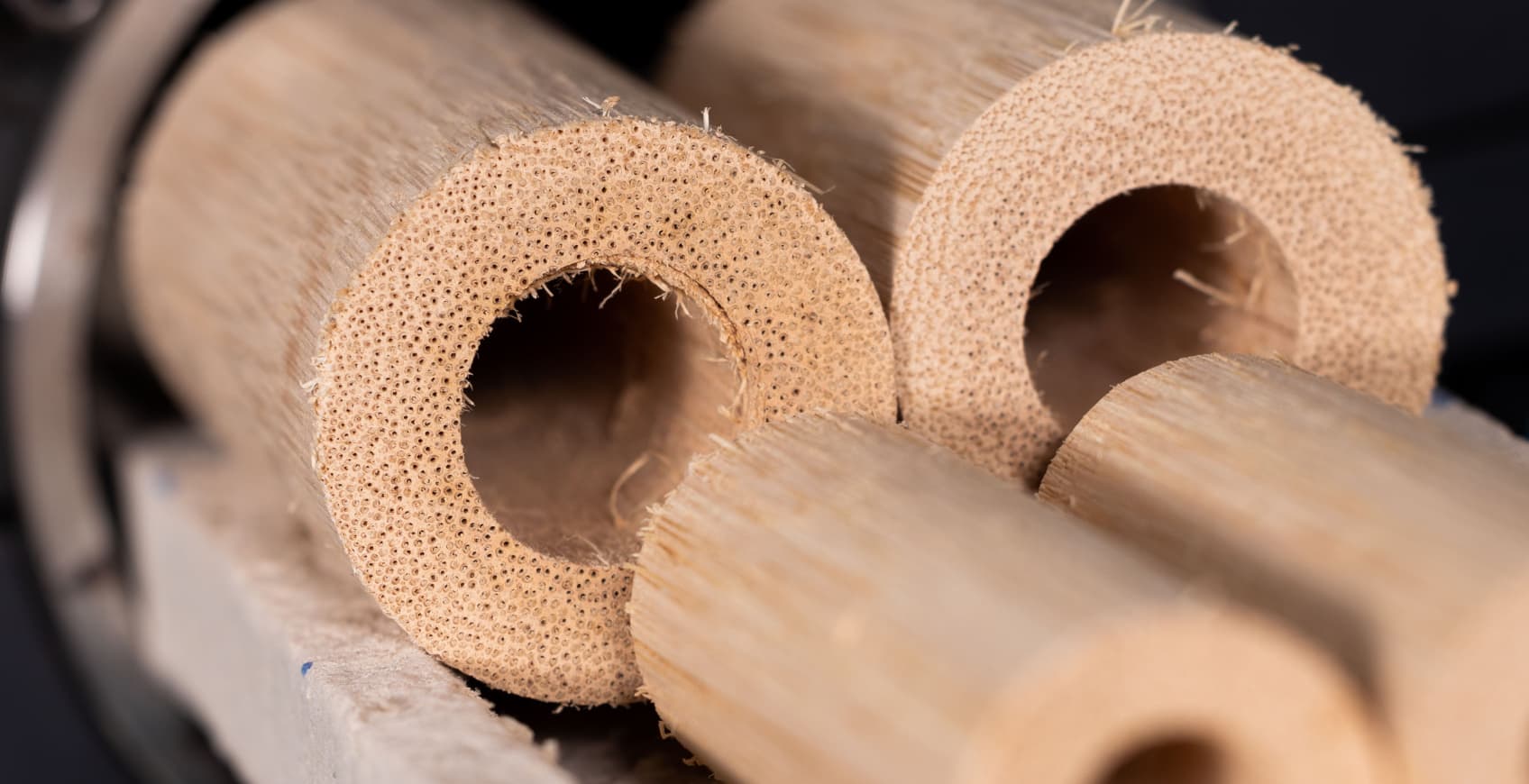
Our Technology
At GreenBone Ortho, we provide innovative, safe and effective solutions for bone regeneration.
Our team of scientists and chemists were inspired by Nature to develop an innovative biomimetic and bioactive bone substitute to address unmet clinical needs in bone reconstruction.
Specifically, GreenBone chose rattan wood because of its intrinsic structure that mimics human bone.
The research group at ISTEC-CNR (Institute of Science and Technology for Ceramics – National Research Council) in Faenza (Italy) developed an innovative and proprietary physical and chemical process to biomorphically transform rattan wood into a biomimetic bone substitute designed as a driver for bone regeneration (1).
GreenBone Ortho has perfected this technology in order to ensure scale-up and delivery to physicians and patients worldwide.
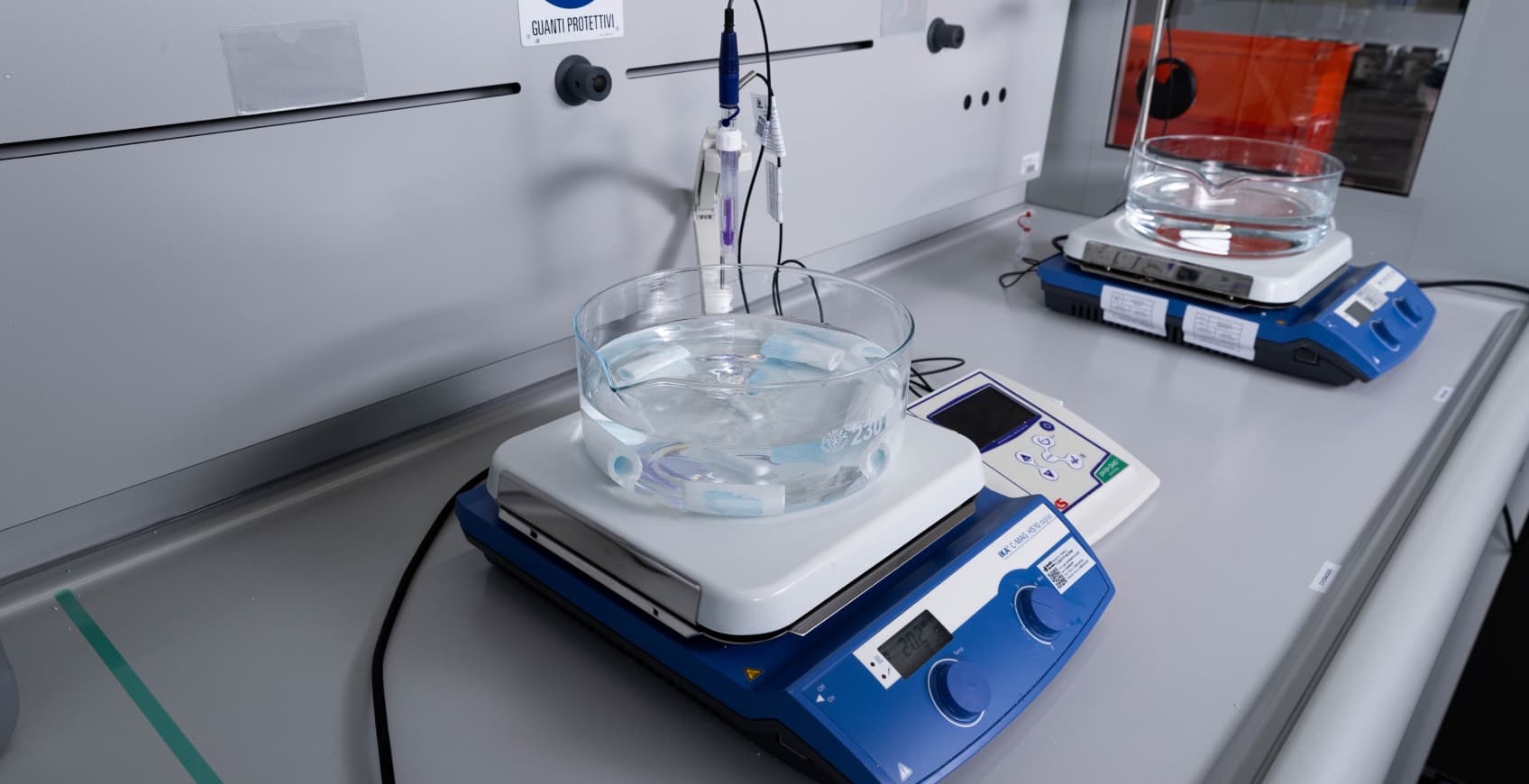
Putting innovation into practice
GreenBone technology includes a novel multi-step process able to transform native vegetable structures into inorganic biomaterial for bone regeneration.
Maintaining the original morphology and hierarchical architecture of the biological template – rattan wood – with pore structures on a micrometer scale. The versatility of this multi-step process allows chemical control of the product and thus the possibility to modulate and improve the bioactivity of the final inorganic material.
The multi-level organized technology of the scaffold ensures vascular remodeling, the proliferation and organization of bone cells as well as satisfying efficient environment for bone cell activities.
Continuous innovation
We are constantly searching for innovation, new applications for our products and building clinical evidence.
For this reason, we collaborate closely with Research Institutes, Universities, and internationally well recognized Key Opinion Leaders to improve best practice and clinical outcomes.
We are commited to developing new products and solutions for orthopedic procedures.
Our Research programs are also focused on developing new applications in the treatment of spinal diseases, osteoporosis, bone infection and bone cancer.
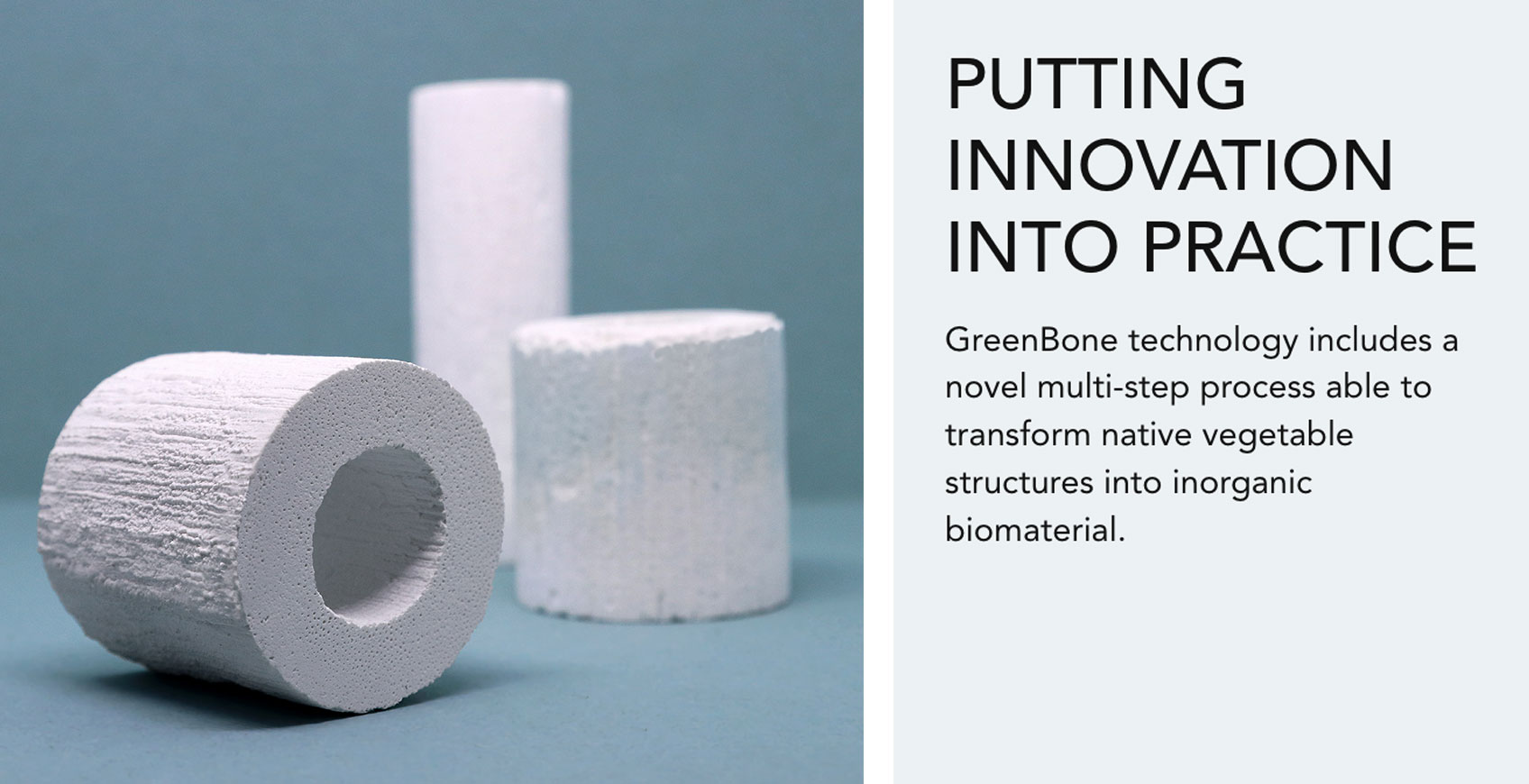
Rattan wood
Rattan is a naturally renewable palm that grows in the tropical regions of Africa and Asia and it has multiple uses, such as for furniture, handicrafts and building material.
Rattan wood was chosen for its microstructural characteristics similar to spongy bone (2) . Rattan wood was selected as a bone model for its outstanding similarity with the structure of osteons, which constitute a main functional unit of the bone hierarchical architecture (3).
GreenBone is committed to the ecological and social sustainability of its source of rattan wood and is collaborating with internationally recognized organizations to ensure environmental sustainability from its activity.
For example, we collaborate with the International Bamboo and Rattan Organization (INBAR), an intergovernmental organization which promotes local partnerships for rattan nursery and proprietary plantations.
In addition to the above initiatives, GreenBone sources its rattan wood from FSC® and SVLK certified suppliers.
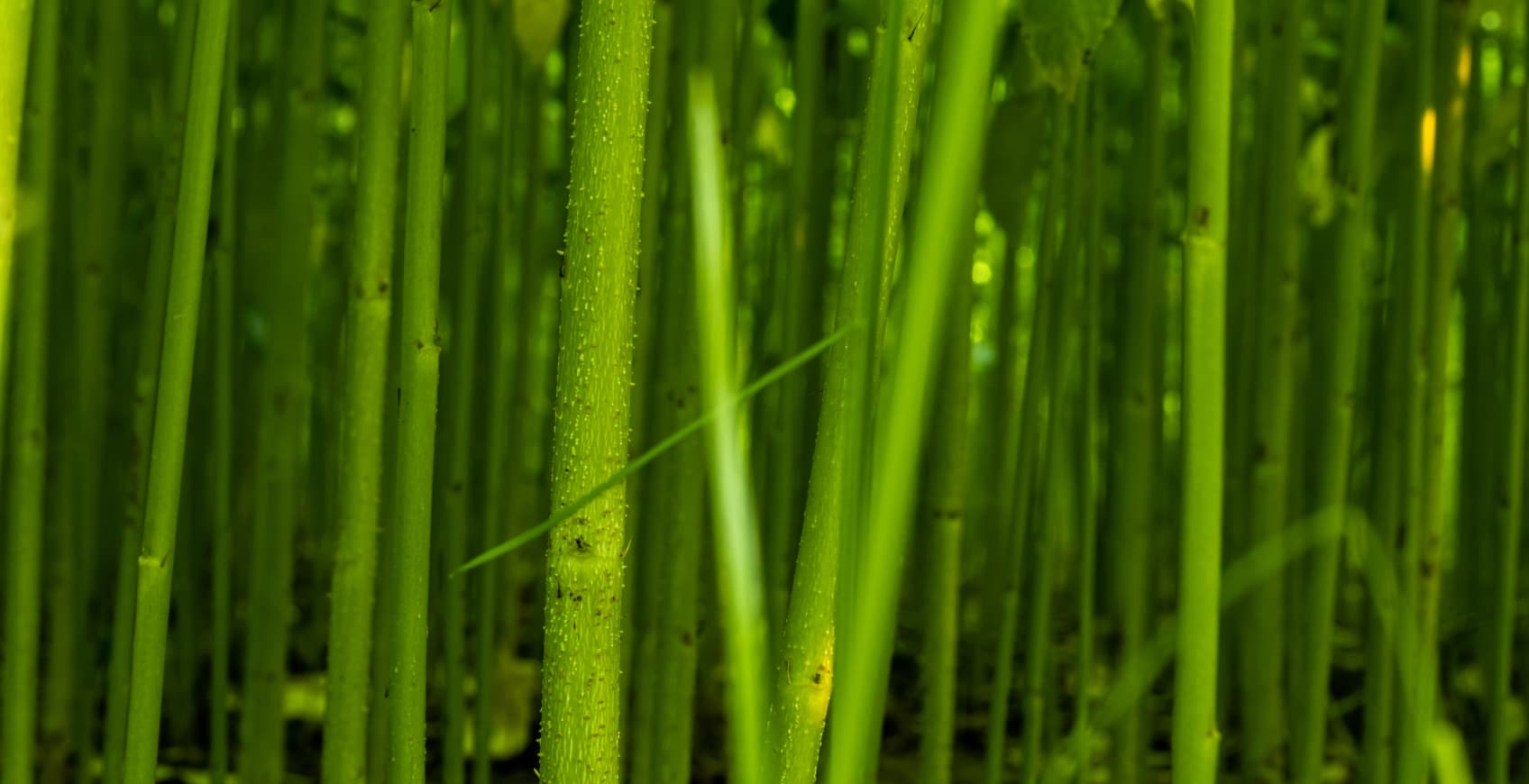
- Tampieri A, Sprio S, Ruffini A, Celotti G, Lesci IG, Roveri N. From wood to bone: multi-step process to convert wood hierarchical structures into biomimetic hydroxyapatite scaffolds for bone tissue engineering. J. Mater. Chem., 2009, 19, 4973–4980
- Ruffini A, Sprio S, Tampieri A. Study of the hydrothermal transformation of wood-derived calcium carbonate into 3D hierarchically organized hydroxyapatite. Chemical Engineering Journal 217 (2013) 150-158
- Ruffini A, Sandri M, Dapporto M, Campodoni E, Tampieri A, Sprio S. Nature-Inspired Unconventional Approaches to Develop 3D Bioceramic Scaffolds with Enhanced Regenerative Ability. Biomedicines. 2021 Jul 29;9(8):916